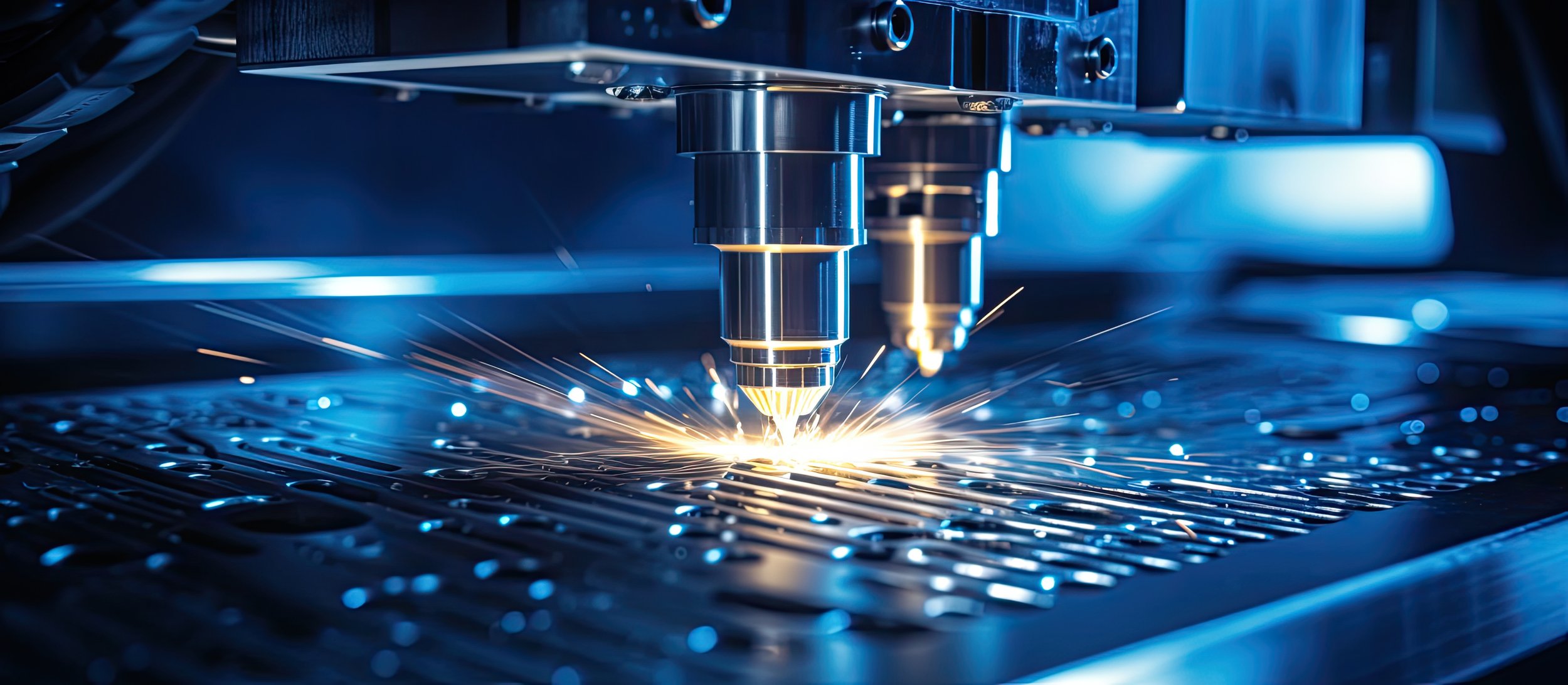
Value Proposition
Us vs. Traditional Blanking
High Speed Digital Laser Blanking is M4.0 enabling:
Lower operating cost.
Light-weight digital manufacturing – (lower upfront investment, speed to market)
Near location supply chain.
BWD Unique Value Propositions to Customers
We deliver cost savings, BIC quality, and minimize investments for low-cost derivatives.
Cost Savings - Material costs savings with increased utilization
Material Utilization Design (MUD) shared saving with customers
Material yield optimization with intelligent nesting – Scrap reduction and offal usage
Master coils instead of slit coils or nonstandard coils
Quality Improvement – eliminate rework and quality issues at stamping plants
No burrs, no micro fractures, etc. – reduced rework and no trimming
Reduced surface damages and less dirt on surfaces on outer panel (class A) blanks
Superior edge quality and mechanical properties
Investment Efficiency – Support low-cost derivatives strategy
Flexibility and metal agnostic – Steel, Stainless, AHSS, UHSS etc.
Upfront engineering blank design and nesting optimization to maximize cost savings at Start of Production (SOP)
Faster Speed to Market – BWD Flexible manufacturing approach
Reduces capital expenditures with blank dies
BWD digital approach handles variants and complexity without the associated cost penalties
Eliminate tool refurbishment cost and tooling engineering changes
Support sustainability and carbon footprint mission
Clean sustainable technology with very lean carbon footprint
Lower energy usage per blank
Cost Benefits
Lower Total Cost of Ownership (TCO) compared to alternatives
• Near net shape “edge-to-edge” blanking
• Optimized in coil arrangements
BWD eliminates the need for physical die change overs and delivers inline production cutting speeds.
BWD delivers superior cut edge quality and blank cleanliness across all materials (especially for advanced high strength steels). Laser welding ready edges do not require an additional precision shearing operation.
BWD eliminates die amortization and maintenance costs.
Competitive Advantages
High Tech Laser Blanking
Speed To Market
Manufacturing Agility
• Provides platform for ideal blank shape and nesting. Increasing material utilization up to 5%
• Delivers superior edge quality across all materials (critical for adv. high strength steels, aluminum)
• Reduces direct labor requirement (operators/material handlers) versus conventional process
• No dies investment, die storage or die maintenance.
• Change perception of critical blank shape capability
• Integrate with laser welding of multiple monolithic blanks removing to improve yield
• Blanking as a service business model
To Be Determined via future partnership and joint efforts
Platform Lifecycle Savings
• $11-22 million from material utilization
•. $3 million in die cost reductions
• $5 million in logistics freight & inventory
• Transitions seamlessly from part run to part run, single coil batch runs.
• Minimizes pallet change over via modern high-speed stackers with robot assist and CNC programming
• Supports multi-blank within coil manufacturing
• Reduces non-value added scheduling and prep administrative activities
• Eliminates die & tooling engineering from critical path
• Simultaneous & iterative multi blank shape concept testing
• Supports blank performance testing via CAD/ simulation capabilities (no hard tool tests). Fast Trial Validation.
• Critical path lead time
• Concept to blank turnaround
• Minimized design and test material usage
• 10% processing speed improvement
(uptime & material handling)
• 20% reduction in indirect on-value added time
Future Product & Process Improvement
Material Utilization & Resource Efficiency
Laser and Stacker specs
Laser and Stacker specs are Best In Industry: Productivity and Quality
Fiber Optic Laser Specs
Bandwidth of 0.2mm. Focus point
Higher power at 4 kilowatts.
LB Mill Edge = 8mm/edge
5 axis (up, down, front, back, angled)
Compressed Air to cut (min. dust)
Stacker – 2 drop stacker
Current Lasers in NA
Bandwidth of 4.0mm
Power 2 kilowatts
Mechanical slit Mill Edge = 10 mm/edge
2 axis
Nitrogen to cut
Single or manual stacking
Quality: Delivers BIC Blank Cleanliness
Our System Approach
Clean room – eliminates sources of contamination.
Double washers, before and after laser box.
Laser technology that delivers burr-free blanks.
Vacuum system and compressed air to extract all dust
Best In Industry washer systems remove all containments down to 15 microns. (Hair = 15 microns)
Material Utilization Improvements
Our System Approach
Clean room – eliminates sources of contamination.
Double washers, before and after laser box.
Laser technology that delivers burr-free blanks.
Vacuum system and compressed air to extract all dust